(postscript ->)The book "A New Era of Knowledge Manufacturing" is now available.)
Sixty years have passed since Peter Drucker proposed the concept of the "knowledge worker" as opposed to the "manufacturing" worker, and the value of manufacturing is also shifting to "knowledge. In May 2020, LIVERNESS, a knowledge manufacturer, will launch its Manufacturing Development Division to redefine the manufacturing platform in Japan, where the traditional manufacturing industry has been stagnant, to evolve into a development center that leverages knowledge.
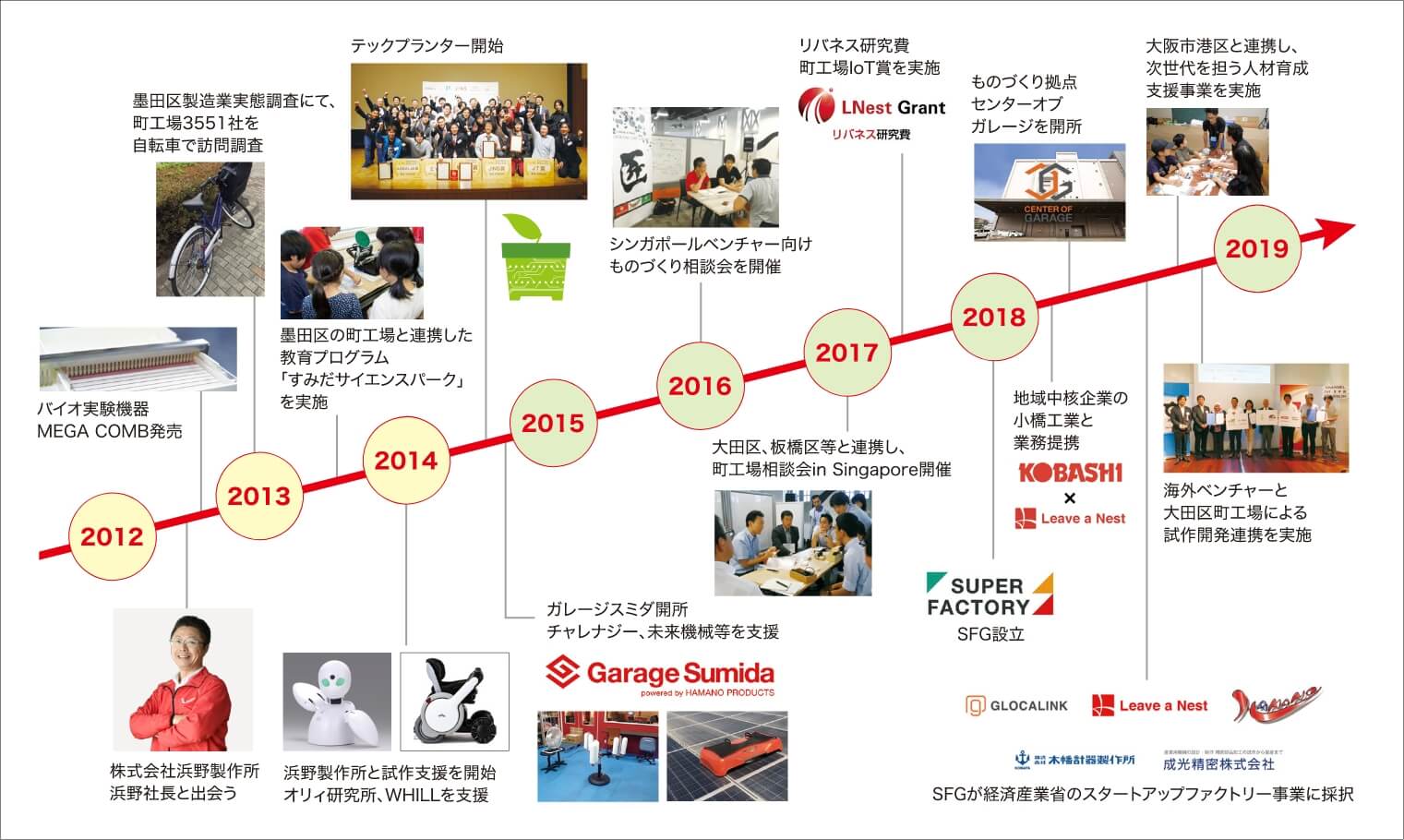
The ever-changing manufacturing industry
Over the past 50 years or so, the environment surrounding the Japanese manufacturing industry has continued to change dramatically. After the era of mass production and mass consumption typified by Japan's high economic growth, local production overseas has expanded and global supply chains have been established, while the hollowing out of the domestic manufacturing industry has become a cause for concern. In addition, since Chris Anderson's book "MAKERS" was released in 2012, the number of venture companies entering the manufacturing industry has increased rapidly, and the boundary between goods and services has been diluted by the IoT, resulting in a drastic change to a society based on the information society, including high-mix low-volume production and sharing economy. The digitalization of business and manufacturing is being implemented to realize a society based on information society. In contrast to Western manufacturers that have implemented digitalization and clearly separated management and manufacturing (factories), the Japanese manufacturing industry, which once thrived through field-oriented improvement activities as typified by Toyota's Kanban system, has been unable to adapt to changes in the information society, and many Japanese companies are now falling behind in terms of productivity. At the same time, local factories, which in the past supported the industry as subcontractors to major firms and grew together with them, are facing the hardship of declining orders and are being asked to break free of their subcontracting nature. What both large firms and local factories have in common is a thirst for new and unconventional manufacturing, which can be summed up by the word "innovation.
What it takes to get out of subcontracting
What exactly is unconventional manufacturing? The clue lies in the "knowledge worker" proposed by Peter Drucker, a well-known management scholar, in his 1960 book "The New Reality. The knowledge worker is a worker who creates new added value through knowledge, in other words, a "knowledge worker," and was described as a contrast to the simple factory labor performed in Western-style manufacturing. The new manufacturing is not manufacturing based on simple factory labor, but manufacturing that focuses on knowledge labor, such as early detection of defects in the development stage, streamlining set-up and manufacturing processes, and obtaining manufacturing patents.
Rivanes came to this conclusion in the course of deepening its relationship with the manufacturing industry since 2012. The grand mission of "disrupting the structure of the traditional manufacturing industry and building a new manufacturing platform" began with one engineering employee who said, "I have not been able to properly explain the field of town great technology and experience. In Japan, I want to work with factories," was his passion. He came up with an idea to change the shape of laboratory equipment used in bio-research into one that would be more efficient with a little ingenuity, and asked a local factory he happened to meet, Hamano Seisakusho in Sumida-ku, Tokyo, to manufacture it for him. At the time, we had no manufacturing know-how, so we told them the purpose and intended use of the product and left the manufacturing method and shape to them. As a result, the "MEGA COMB," a bio lab equipment with the desired functions but with fewer processing steps and at a lower cost by far, was born. At this time, they realized the importance of communication in order to draw out the extent of the manufacturing knowledge of the local factories, and saw great potential in the teamwork between the local factories and RIVERNESS' Science Bridge Communicators®.
Business practices prevent knowledge from being manifested
However, at the same time that we see the potential, we also identify the reasons that hinder the manifestation of knowledge by town factories: In 2013, at the request of Sumida Ward, we purchased 10 bicycles and conducted a survey of all 3551 businesses in the ward over the course of one summer. While there were many town factories with great technology and experience, knowledge that can help solve problems in the field, we witnessed many town factories that felt stuck in their operations. While many of them were facing challenges in developing sales channels, more than half of them had no idea of new business, and it became clear that they were unable to get out of the framework of their existing businesses. The most important issue was the business practice of estimation in the Japanese manufacturing industry. Even though many of the local factories add value in planning and design, estimates are calculated based on the unit cost of parts x quantity. As a result, for example, if one compares the quotation given by an overseas venture to a factory in China or Vietnam with the quotation given by a Japanese factory, the price of the same part would be several times higher in the Japanese case. In fact, there is a difference between the overseas factories, which quote the manufacturing cost as the cost of parts for the drawings they are told, and the Japanese factories, which provide knowledge that can solve the manufacturing problems that the venture is having, and add value through knowledge labor other than the cost of parts. By including it in the cost of parts, they are unable to properly explain the added value they are providing. This way of estimating, which has become the norm in Japan due to the influence of the supply chain led by major companies, or in other words, the business practice of not attaching value to knowledge, has become a stumbling block for the Japanese manufacturing industry to make a leap forward.
Town factories can be partners in ventures.
Machi Factories Can Become Partners for VenturesHow can the added value of knowledge-based labor in the existing manufacturing industry, especially in machi factories, be made apparent? In order to solve this problem, Hamano Seisakusho and LEVANES started a new business in collaboration to provide "prototyping support for venture companies. With the cooperation of Sumida Ward, Hamano Manufacturing converted part of its premises into a venture incubation facility. Using this facility, named "Garage SUMIDA," the company supported the prototyping of WHILL, a next-generation electric wheelchair, and Oly Laboratory, an alter-ego robot, both of which were still unknown at the time. A major turning point for this project came at the first Tech Plan Grand Prix held in March 2014. Mr. Atsushi Shimizu (current president of Chalenazy Inc.) won the Grand Prize for this initiative, in which Mr. Hamano, president of Hamano Seisakusho, participated as a judge. At the time, he had just started his own business, had no friends, and did not have ample funds. Hamano Manufacturing offered Garage Sumida as a home base for him and supported his manufacturing from the ground up. The company was selected for NEDO's "Research and Development Venture Support Program," which was launched at that time, and developed a prototype for PoC with the business funds received as an extra prize for winning the Tech Planter competition. The prototype attracted attention from business companies, the media, and VC firms, and the money raised was used to work with Hamano Seisakusho again on manufacturing. Hamano Seisakusho was close to the manufacturing challenges faced by Charenergy at every step of the process, and continued to solve them as a partner rather than a subcontractor. The company successfully raised funds from a VC firm, developed a 10kW machine and installed it on Ishigaki Island for demonstration purposes, and established a joint venture with a Philippine state-owned company for demonstration purposes in the Philippines. This is proof that local factories can become partners with venture companies and that they can create knowledge-based value.
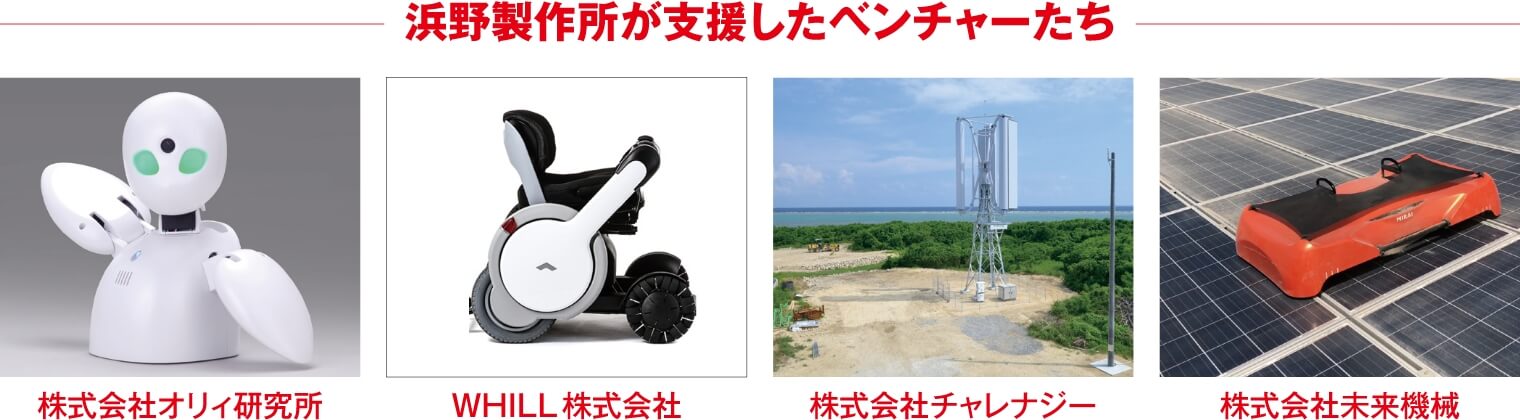
A group of super-machine factories spread throughout Japan
In 2015, just as "Shitamachi Rocket" became a big hit on TV, this story of a town factory growing in partnership with a venture was picked up by various media and rapidly gained recognition. Since then, many ventures have accelerated their manufacturing with Garage SUMIDA's support, including Miraikikai, which develops solar panel cleaning robots, and drone venture Aeronext In 2018, Garage SUMIDA's efforts won the Minister of Economy, Trade and Industry Award at the 7th Monodzukuri Nippon Grand Awards. Furthermore, the importance of Garage Sumida has been recognized nationwide, with the Emperor Heisei visiting Garage Hamano Seisakusho as a "venture support facility.
In the same year, RIVANES and its subsidiary GLOKA LINK opened the "Center of Garage," a venture incubation facility specializing in manufacturing in Sumida-ku, Tokyo, to establish a base for connecting local factories and manufacturing ventures from around the world. Then, with a desire to share Hamano Manufacturing's know-how and successful experience with many local factories and to support aspiring factories, he established the Super Factory Group (hereafter SFG) together with Hamano Manufacturing and began the challenge of expanding the Garage SUMIDA brand to other regions. Unique town factories include Garage Taisho (operated by Kibata Keiki Seisakusho Co., Ltd.), which specializes in medical-industrial collaboration, Garage Ota (operated by Sankei Engineering Co., Ltd.), which is a specialist in thermal fluidics, and Garage Minato (operated by Nariko Seimitsu Co., Ltd.), whose strengths lie in regional collaboration, including with non-manufacturing industries. (operated by Seikou Seimitsu Co., Ltd.), which has strength in regional cooperation including non-manufacturing. Each is taking on the challenge of manufacturing products that make the most of their own characteristics, and through the sharing of their know-how, they are realizing mutual growth.
SFG has been selected for the "Startup Factory Construction Project," a project by the Ministry of Economy, Trade and Industry to break through the "mass production barrier" by establishing a support base for design and prototyping for mass production of startups, etc. SFG has been recognized as one of the leading venture support groups in Japan that has produced many successful cases. The company has been adopted by the Ministry of Economy, Trade and Industry's "Startup Factory Construction Project". The fact that local factories can become partners in venture businesses is now becoming a common concept. And the program has expanded into mid- to long-term activities to revitalize the manufacturing industry, such as identifying overseas needs and implementing educational programs for the next generation, in cooperation with Sumida, Ota, and Itabashi wards in Tokyo and Minato Ward in Osaka, among other local governments.
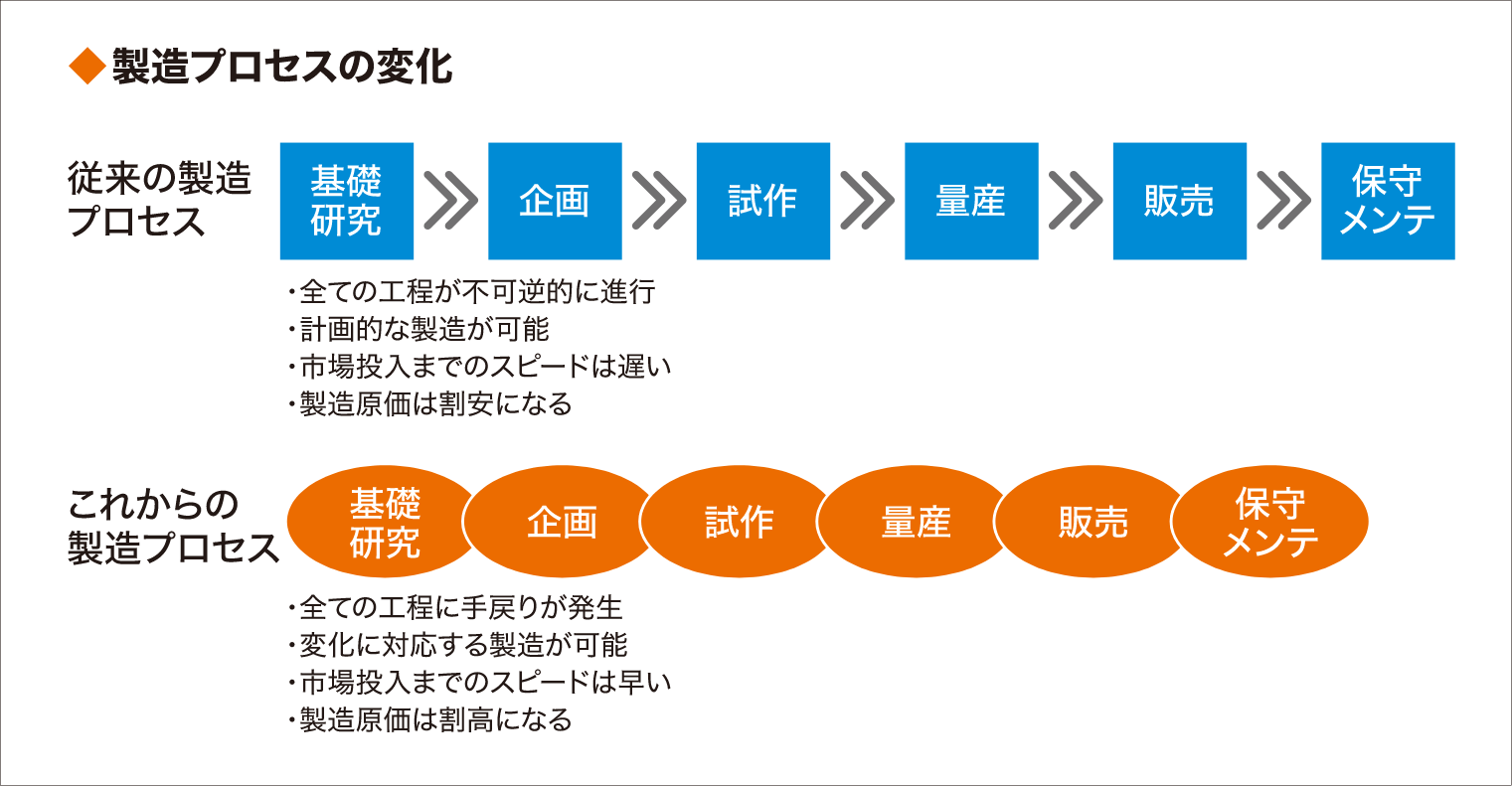
The next barrier is "mass production.
Although the optimum solution for supporting prototype production of venture businesses has been found through collaboration with local factories, the next issue that has been raised is the "barrier to mass production. This issue is one that SFG continues to explore through trial and error. In recent years, major companies have begun to provide mass production support to venture businesses by using their vacant factories, but there have not yet been enough success stories reported. Against this background, RIVERNESS has continued to consider what the "barrier to mass production" is. While the focus is generally on the difficulty of crossing the gap between prototype and mass production, we have noticed that the term "mass production" has different meanings depending on whether it is used by a local factory (parts processor), a large corporation (manufacturer), or a venture company. For example, for a small factory, mass production is the process of manufacturing multiple uniform products, while for a large company, it is the process of continuing to manufacture and sell multiple uniform products. In contrast, for venture companies, the term "mass production" often refers to the next phase of manufacturing after prototyping and does not or cannot take into account how long they will continue to manufacture and sell the same products thereafter. Due to this difference, even if a local factory provides support, it cannot assist in determining the optimal specifications because it has no concept of sales. In large companies, the process of profit development, prototyping, mass production, and sales, which is generated by sales for decades after mass production, proceeds irreversibly and generates profit over a long period of time after mass production. However, in the case of venture companies, new prototype ideas are generated in the middle of mass production, causing rework, and furthermore, the process of reviewing the product specifications themselves due to changes in awareness of issues may occur in parallel. Above all, there is no guarantee as to how long the manufactured product will continue to sell. In other words, the barrier to mass production is not a problem of quantity, but rather a communication gap between the traditional manufacturing model based on mass production and mass consumption (town factories and traditional manufacturers) and the new manufacturing model (venture companies) based on the information society, including high-mix, small-lot production and the sharing economy. The conclusion is that there is a communication gap between the planning/designer and the factory. Compared to manufacturing overseas, where the division between planning and designers and factories is clearly defined and factories are characterized by faithful adherence to the instructions of designers, this friction is particularly large in Japan, where factories, from small factories that manufacture parts to large companies that serve as manufacturers, have strong know-how. However, if we can bridge this gap, we should be able to establish a new model of manufacturing as knowledge-based labor that cannot be imitated by other countries.
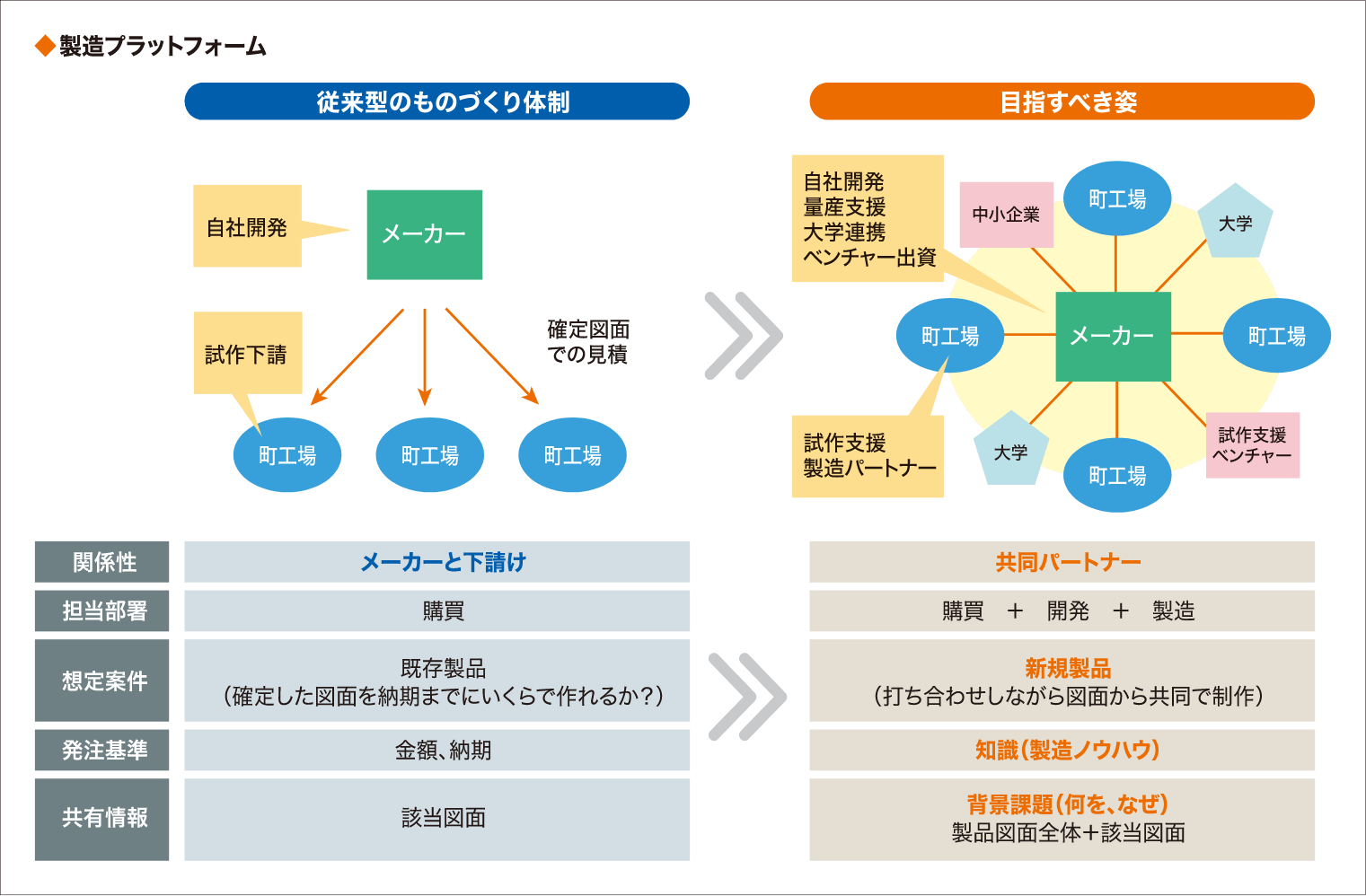
Top niche manufacturers that form the core of the region are the key.
On the other hand, a third force in venture support that we have seen in the regional tech planters that LIVERNESS has developed in the region are top niche manufacturers that have characteristics that differ from both local factories and large corporations. These companies are manufacturers with the No. 1 market share in a particular niche, and under the leadership of the owner-president, they develop everything from R&D to sales on their own. They have a network of local town factories that specialize in parts processing and are positioned as drivers of the local economy. In addition, decision-making is faster than at large companies, and the company's small size facilitates cooperation among departments such as development, purchasing, manufacturing, and sales. Kobashi Kogyo, which manufactures and sells agricultural machinery and parts in Okayama Prefecture, promotes collaboration with venture companies such as Euglena and Aeronext, and has invested in several venture companies. With sales ranging from several billion yen to several tens of billions of yen, Kobashi Kogyo has the potential to achieve growth beyond that of today's large companies through collaboration with venture companies.
A manufacturing platform that realizes everything from prototype development to mass production in various regions has emerged as a pathway for the integration of local core manufacturing companies such as Kobashi Kogyo, which has the ability to guarantee quality and flexibility for mass production, in addition to local factories with high design capabilities and specialized technologies. It will be essential to create a mechanism based on knowledge-based manufacturing, rather than one based on the optimization of conventional manufacturing. To achieve this, it is necessary to solve various issues, such as building a relationship as a partner that is different from the subcontractor relationship between a large company and a local factory, organizing the added value of the manufacturing industry that should be expressed in estimates, building a mass production model that is optimal for venture companies, and how to collaborate with universities. The new manufacturing platform that lies ahead of solving these issues should push the manufacturing industry into a new phase.
Realization of Inbound Globalization
Will the new manufacturing platform work globally? In 2017, we took President Hamano of Hamano Mfg. to the Tech Planter in Southeast Asia, which had begun at that time, and started a town factory consultation session for seven of the ventures that had appeared in the final round in Singapore and had an awareness of the challenges they faced in manufacturing. The ventures brought in various consultations, which were translated by RIVANES members and answered by President Hamano. Among the cases, President Hamano responded "it cannot be done" in only one case, which was impossible according to the laws of physics, and many of the consultations were not difficult for Japanese machi-factories. Furthermore, in 2018, the "Project to Investigate the Possibility of Creating Collaborations between Companies in the Ward and Overseas Venture Businesses" will be launched, commissioned by Ota Ward. Under this project, Ota City provided subsidies for prototype development costs and support for prototype development for overseas ventures, with the aim of solving the manufacturing issues faced by overseas R&D ventures using the know-how and technology of Ota City's machi-factories. Three ventures from six Southeast Asian countries, selected from 52 applications, and Ota Ward factories with strong networks worked together for about six months to develop prototypes, resulting in prototypes that were satisfactory for the overseas ventures. What these results lead to is the fact that the manufacturing knowledge possessed by advanced manufacturing businesses can be used to develop the "deep tech" needed to solve deep issues lying in Southeast Asia. By attracting Southeast Asian ventures to Japan and fusing the region's core top niche manufacturers with super factories, issues from prototyping to mass production can be solved seamlessly. The resulting products will be used by Southeast Asian ventures to spread their wings to the rest of the world. In the future, when inbound globalization that links Japan with the market of 650 million people in Southeast Asia and creates new value is realized, the era in which manufacturing companies sell knowledge will become commonplace.
(Text: Kazuhiro Hasegawa)
Source: Hasegawa, K. (2020). Supporting Foundations 18, 11-16.
New Business Development Seminar
[Creating a business to solve a problem with 3000 venture 3000 researchers].
ABCDE Theory" for creating new businesses
Case studies of knowledge manufacturing initiatives